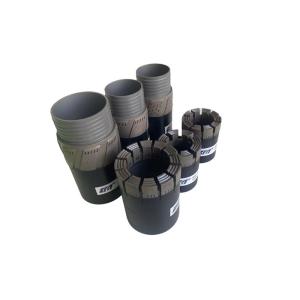
Add to Cart
Minimized jamming and clogging reduced wear on drill bits Diamond Reaming Shell
More details about diamond reaming shells in core bit drilling, mining, and geological exploration:
Reaming Shell Customization: In some drilling applications, custom-designed reaming shells may be necessary to meet specific requirements. Manufacturers can work closely with drilling operators to create tailored reaming shells based on factors such as rock formation characteristics, drilling conditions, and desired performance outcomes. Customization can involve modifications to the diamond impregnation pattern, flushing hole configuration, or overall design of the reaming shell.
Reaming Shell Performance Analysis: Drilling operators often conduct performance analysis of reaming shells to assess their effectiveness and make informed decisions. This analysis may involve monitoring drilling parameters, such as penetration rate, torque, and vibration, to evaluate the performance of the reaming shell. By analyzing these data, operators can identify areas for improvement, troubleshoot issues, and optimize drilling operations.
Reaming Shell Safety Considerations: Safety is a critical aspect of any drilling operation. When using diamond reaming shells, it is essential to follow safety protocols and guidelines to minimize the risk of accidents or injuries. This includes wearing appropriate personal protective equipment (PPE), conducting regular equipment inspections, and adhering to safety regulations and industry best practices.
Reaming Shell Transportation and Storage: Proper transportation and storage of diamond reaming shells are necessary to maintain their integrity and performance. Reaming shells should be protected from damage during transit and stored in a clean and dry environment to prevent corrosion or contamination. Following manufacturer recommendations for transportation and storage practices helps ensure the longevity of the reaming shells.
Reaming Shell Innovations: The field of diamond reaming shells continues to see innovations aimed at enhancing performance and efficiency. These innovations may include advancements in diamond impregnation technology, improvements in flushing systems, development of new materials, or the integration of smart technologies for real-time monitoring and control. Ongoing research and development efforts drive these innovations to meet the evolving needs of the drilling industry.
Reaming Shell Applications Beyond Drilling: While diamond reaming shells are primarily associated with core bit drilling, their applications extend beyond this field. Reaming shells can be used in other industries such as construction, civil engineering, and geotechnical investigations. In these applications, reaming shells are employed to create boreholes for various purposes, such as installing foundation piles or conducting soil sampling.
Reaming Shell Optimization Software: Computer-aided design (CAD) and simulation software tools are utilized to optimize reaming shell design and performance. These software tools enable engineers to analyze and refine various aspects of the reaming shell, such as flushing patterns, impregnation placement, and fluid dynamics. By simulating drilling conditions and analyzing the data, engineers can optimize the design to achieve better cutting efficiency and improved drilling performance.
Reaming Shell Cost Considerations: The cost of diamond reaming shells can vary depending on factors such as size, design complexity, diamond impregnation quality, and brand reputation. While cost is an important consideration, it is crucial to strike a balance between affordability and quality. Choosing high-quality reaming shells that offer durability and performance often proves more cost-effective in the long run, as they tend to last longer and require fewer replacements.
In summary, diamond reaming shells are versatile tools used in various drilling applications. Customization, performance analysis, safety considerations, transportation and storage practices, and ongoing innovations are important aspects of using reaming shells effectively. Software tools aid in optimizing reaming shell design, and cost considerations should be balanced with the quality and longevity of the reaming shells.
Specifications
ITEM | DIAMOND BIT | Reaming shell | |||||
"Q" Series Wireline assembly | Size | Bit Outer Diameter | Bit Inner Diameter | ||||
mm | inch | mm | inch | mm | inch | ||
AQ | 47.60 | 1.88 | 26.97 | 1.06 | 48.00 | 1.89 | |
BQ | 59.50 | 2.35 | 36.40 | 1.43 | 59.90 | 2.36 | |
NQ | 75.30 | 2.97 | 47.60 | 1.88 | 75.70 | 2.98 | |
HQ | 95.58 | 3.77 | 63.50 | 2.50 | 96.00 | 3.78 | |
PQ | 122.00 | 4.80 | 84.96 | 3.35 | 122.60 | 4.83 | |
Metric T2 Series | 36 | 36.0 | 1.417 | 22.0 | 0.866 | 36.3 | 1.429 |
46 | 46.0 | 1.811 | 32.0 | 1.260 | 46.3 | 1.823 | |
56 | 56.0 | 2.205 | 42.0 | 1.654 | 56.3 | 2.217 | |
66 | 66.0 | 2.598 | 52.0 | 2.047 | 66.3 | 2.610 | |
76 | 76.0 | 2.992 | 62.0 | 2.441 | 76.3 | 3.004 | |
86 | 86.0 | 3.386 | 72.0 | 2.835 | 86.3 | 3.398 | |
101 | 101.0 | 3.976 | 84.0 | 3.307 | 101.3 | 3.988 | |
T Series | TAW | 47.6 | 1.875 | 23.2 | 1.31 | 48.0 | 1.89 |
TBW | 59.5 | 2.345 | 44.9 | 1.77 | 59.9 | 2.36 | |
TNW | 75.3 | 2.965 | 60.5 | 2.38 | 75.7 | 2.98 |
FAQ
Q1: How often should a diamond reaming shell be replaced?
A1: Replacement frequency depends on usage and wear, but regular inspection and monitoring can help determine when a replacement is needed.
Q2: Can diamond reaming shells be used in both soft and hard rock formations?
A2: Yes, diamond reaming shells are designed to cut through a wide range of rock formations, from soft to hard.
Q3: What are the common challenges or issues encountered when using diamond reaming shells?
A3: Challenges can include diamond wear, clogging of waterways, deviation control, and maintaining drilling fluid circulation.
Q4: How can I optimize the performance of a diamond reaming shell?
A4: Optimize performance by using proper drilling parameters, maintaining waterway cleanliness, and choosing the appropriate reaming shell for the formation.
Q5: Are there any specific safety precautions to consider when using diamond reaming shells?
A5: Follow standard drilling safety protocols, such as wearing appropriate personal protective equipment (PPE) and ensuring proper equipment handling.